About FAST Global Solutions
DELIVERING ACCELERATED SOLUTIONS AROUND THE WORLD SINCE 1979
For over 40 years, FAST Global Solutions has been helping improve operational performance in the air transportation and material handling industries, with smartly designed and ruggedly built equipment. Founded in 1979 as Watkins Aircraft Support Products (WASP), the company’s focus on unparalleled quality and critical safety engineering of non-powered ground support equipment, resulted in exponential growth—doubling in capacity every year for the first decade.
Production momentum for the company continued over the years, with the addition of package conveyor and military trailer design and manufacturing. In 2015, WASP combined with FAST Manufacturing—a producer of high-quality agricultural sprayers and liquid fertilizer equipment—and rebranded become FAST Global Solutions. In 2020, the ag division was sold to resume focus on the air and ground solutions the company offers.
FAST Global Solutions touches nearly every part of the globe from our Midwest facilities, where high-tech equipment fills the manufacturing floor and engineers design solutions for our customers. Large-scale robotic welders, automated paint processes, plasma laser cutters and large-scale press brakes help employee-owners successfully meet customers’ needs.
Today, FAST Global Solutions is comprised of two product divisions:
GSE – The world’s largest manufacturer of non-powered ground support equipment for the airline and air cargo industry.
Conveyors – A leading manufacturer of parcel conveyor equipment for the material handling industry.
Aftermarket Parts and Service – Your Partner for the Entire Lifecycle of our Equipment.
OUR PURPOSE
Deliver winning solutions to help our customers, communities and employees thrive.
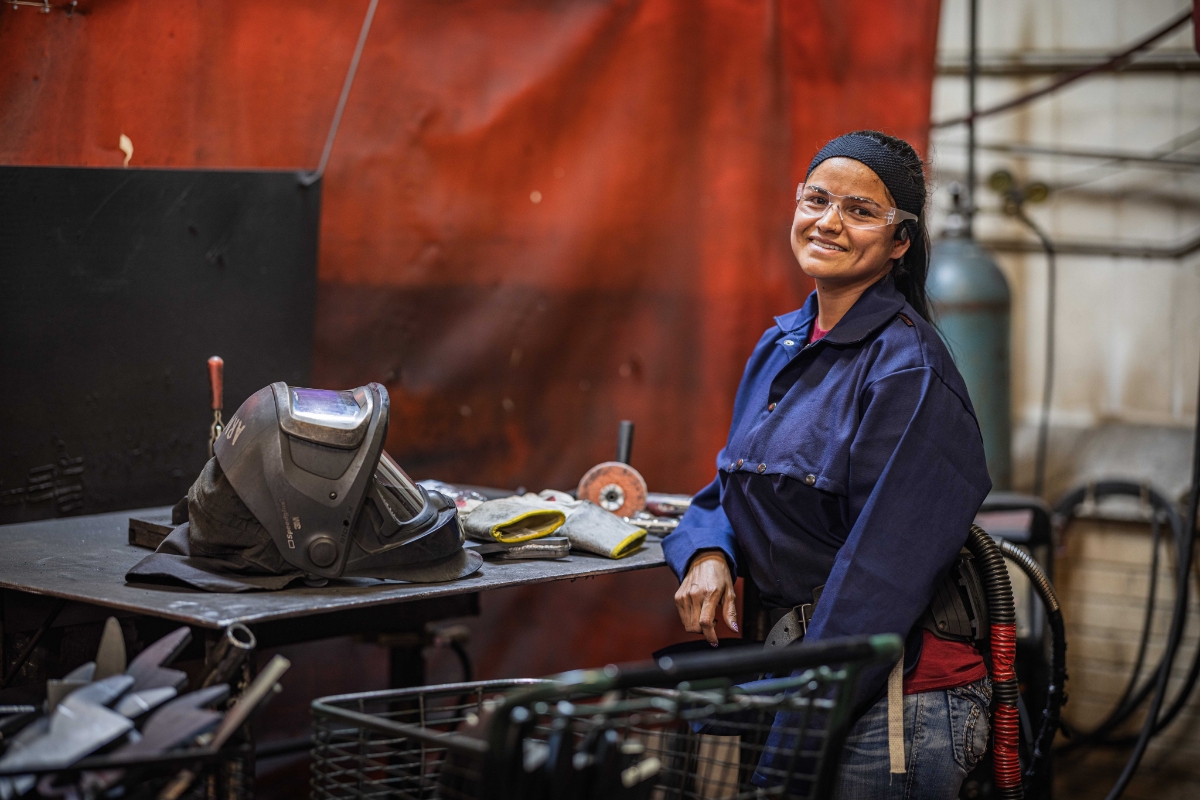
100% Employee Owned
As a 100% employee-owned company, we take pride in our craftsmanship and stand behind every piece of equipment we build. The FAST team, of over 550 employee-owners— including 130 certified welders and an engineering team of over 30 employees with 300 combined years of experience—understands the operational needs of our customers and continues to create ultra-reliable equipment that leads the industry in available uptime, higher performance, and longer lifecycles. We operate to ensure rapid turnaround times for parts and equipment orders, and to meet the exacting standards of each customer’s individual needs.
Operational Performance and Safety
The company established high standards for what we design, engineer and build so that our customers experience minimal maintenance, more uptime and the lowest total cost of ownership.
- Durable materials, premium hardware and advanced design, for equipment that’s ready when you need it and lasts through years of rigorous daily use.
- Perform some of the most demanding product testing in the industry, to ensure our custom-designed equipment is durable and safe to operate.
- Full-time quality inspectors on site to certify all equipment built meets industry and global standards (OSHA, SAE, CE, IATA), and our customers’ individual safety specifications
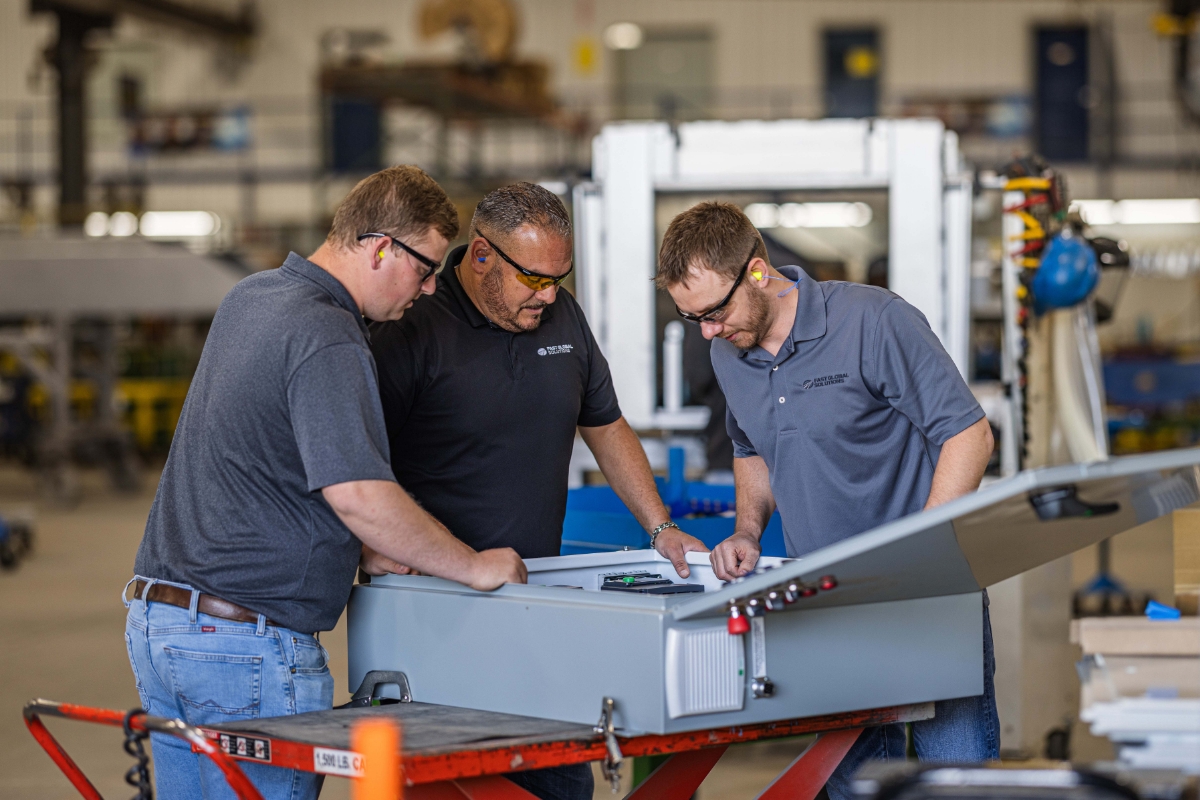
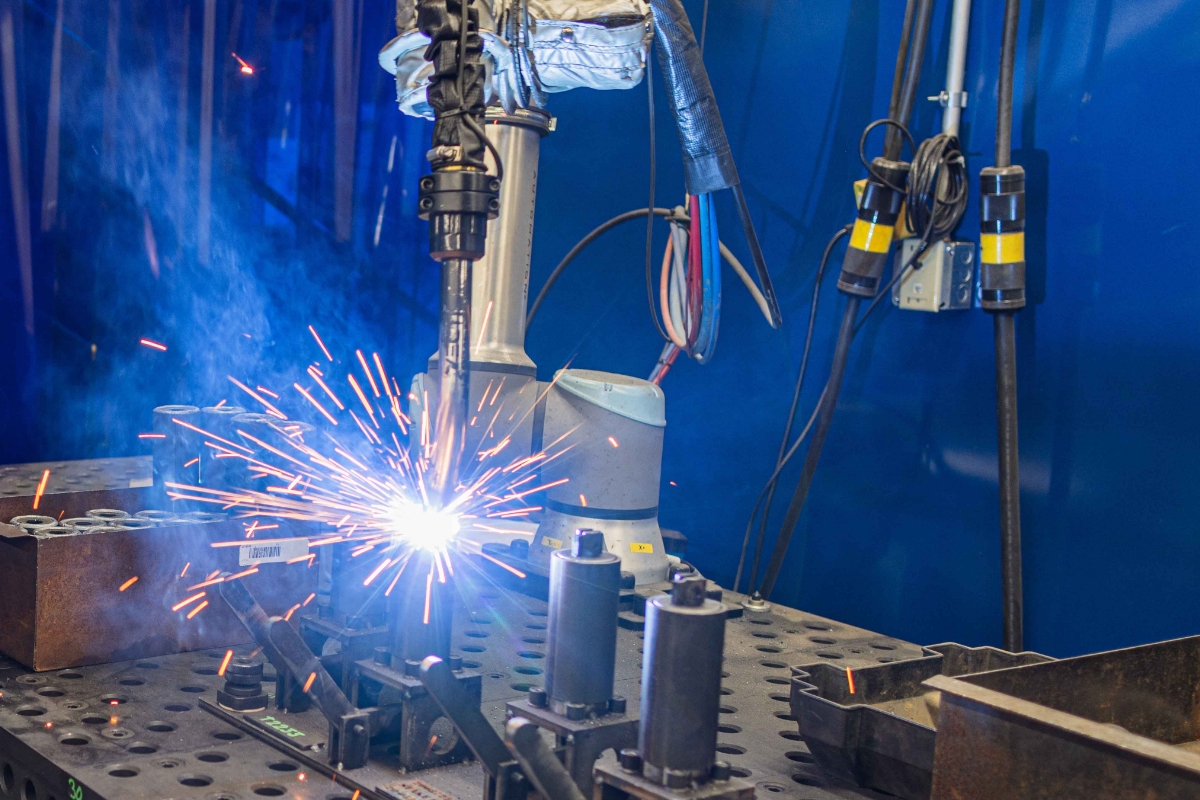
World-Class Manufacturing
To meet the evolving needs of our global customers, we continue to expand our domestic and international operations, scaling capacities, capabilities and resources.
- Eight production facilities worldwide, with over 700,000 sq ft of manufacturing space to be able to fulfill equipment orders quickly.
- Continual introduction of advanced technology, including robotic welders, plasma laser cutters, large-scale press brakes and automated powder-coat paint booths and ovens, to enhance productivity and ensure a consistent level of quality.
- ISO Certified since 2003.
We know downtime in the air transportation and material handling industries costs money, which is why we provide support throughout the entire lifespan of our products.
- Maintain a dedicated parts department, with over 5,000 OEM replacement parts in-stock at all times.
- 95% of all stocked parts orders ship within 24 hours, to quickly get your operations back up to speed.
- Experienced technicians available to provide in-house or on-site support, to help keep you up and running.
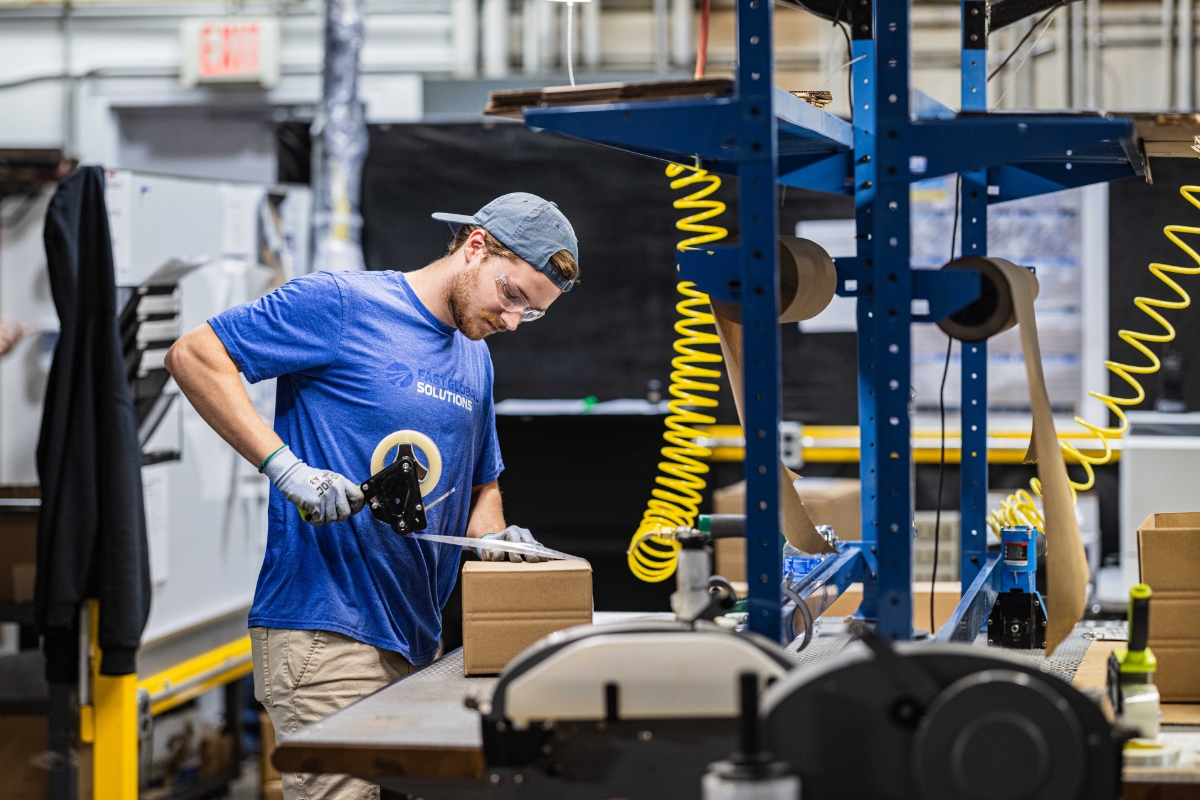